Ready for new quantum leaps.
The Norwegian fish farmer Akvafuture carried out a financial overhaul last year, with major cost cuts and the sale of assets.
“In the last seven years, and after producing close to 30 million kilograms of lice-free salmon, from closed cages, we have learned an enormous amount. Now we are ready to take a quantum leap in the development of closed production at sea,” managing director Thomas Myrholt said.
Out by the octagonal closed cages at the Northern Norway location, he proudly displays the uniqueness of the in-house developed Akvapods. The first fish were released here in 2016, and today there are 75,000 fish in each of the ten cages.
“Last year the company produced around 4,800 tonnes of gutted salmon. This year the number will be significantly lower due to the special harvest plan, which means that this year no fish will be harvested between March and November. Despite this, the result looks good. Close to NOK 50 million (€5 million) in operating profit, and EBIT per kilo of harvested fish of over NOK 20 (€2),” Myrholt said.
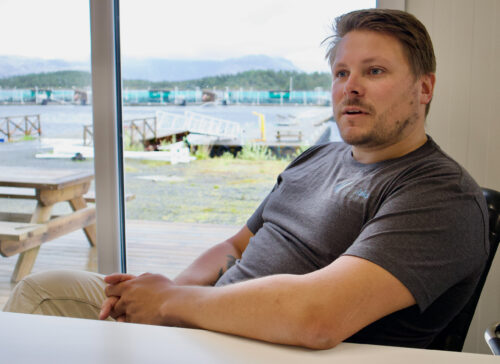
Looking for improvements
At the facility at Sæterosen, a little over half an hour east of Brønnøysund, the three employees can go out to the cages in dry shoes. Here, Ben Øksnes is the operations manager.
He has 20 years of experience from various players in the region, as well as a stay in Chile. Together with the management and the employees, he constantly works to optimize the daily operations.
“There is a constant search for improvement potential. Now we have a particular focus on cleaning and oxygenation, there is more to be gained here in the future. We have learned to run the cages in a more rational and economic way than before. We have reduced the use of diving and flushing, we have reduced it considerably, as well as improved the equipment,” Ben Øksnes said.
At the Hamnsundet site, they are now testing a more dynamic management of the water supply. The cage is “flushed” between meals to constantly provide the most optimal conditions for the fish. It should provide better and more efficient operation, according to Thomas Myrholt. He shows off the very lifeblood of the facility, the water intake.
“Here the lice-free water comes up from the depths, is led through the bag wall and into the cage. Now the speed is low as there are small fish, but with larger fish the speed of the water is increased. The fish get a good trim and grow faster. This is what makes the salmon lice-free, and grows around 12 per cent faster than the average elsewhere in the industry,” Myrholt said.
“What is the disadvantage of this type of cage?”
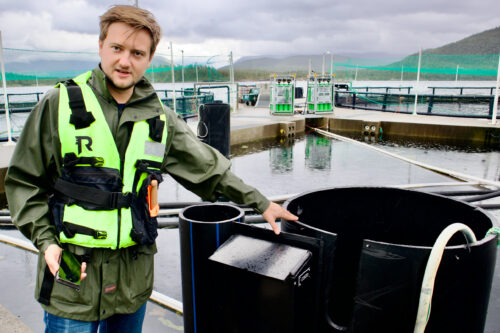
“It’s the amount of equipment. It leads to a good deal of work, which does not happen at other ordinary facilities, Myrholt smiled, showing off most of the technical installation outside the facility.”
“Now we have designed and produced a new oxygen network, with fewer connections than today. It also means that we can raise ourselves to the next level,” he said.
The tight net bag separates them from the others, but for safety’s sake they have fitted an extra net around it.
Not first in the smolt queue
The fish that is out here today is about 400 grams, and was released as a smolt of around 80 grams in May. They would have liked to have bigger smolt.
“To get a better production, we would have liked to have some smolt of 100 grams and something of around 300 grams, that would have been optimal,” Øksnes said.
“As a small independent fish farmer, we’re probably not first in the queue, then we probably won’t get the size and quality we want,” Thomas Myrholt said. It is in the first phase in the sea, Akvafuture is still experiencing high mortality, which they would like to have lower.
Mortality is very low. Only 3.5 percent mortality is the average for the last three years. There is 80 percent lower mortality than in the industry in general. It is soon after release, and as a result of the varying quality and size of the smolt, that mortality is high. “Just over a month after postponement, we hardly have any dead fish in the plant,” Myrholt said.
The cage that stands here today was designed in 2015 and has undergone certain modifications.
“Now we want to build a fourth plant, based on what we have experienced so far. Then we will increase the cages from 90 to 120 metres, which significantly reduces the investment cost per kilo of fish produced. The capacity will nearly triple,” he said.
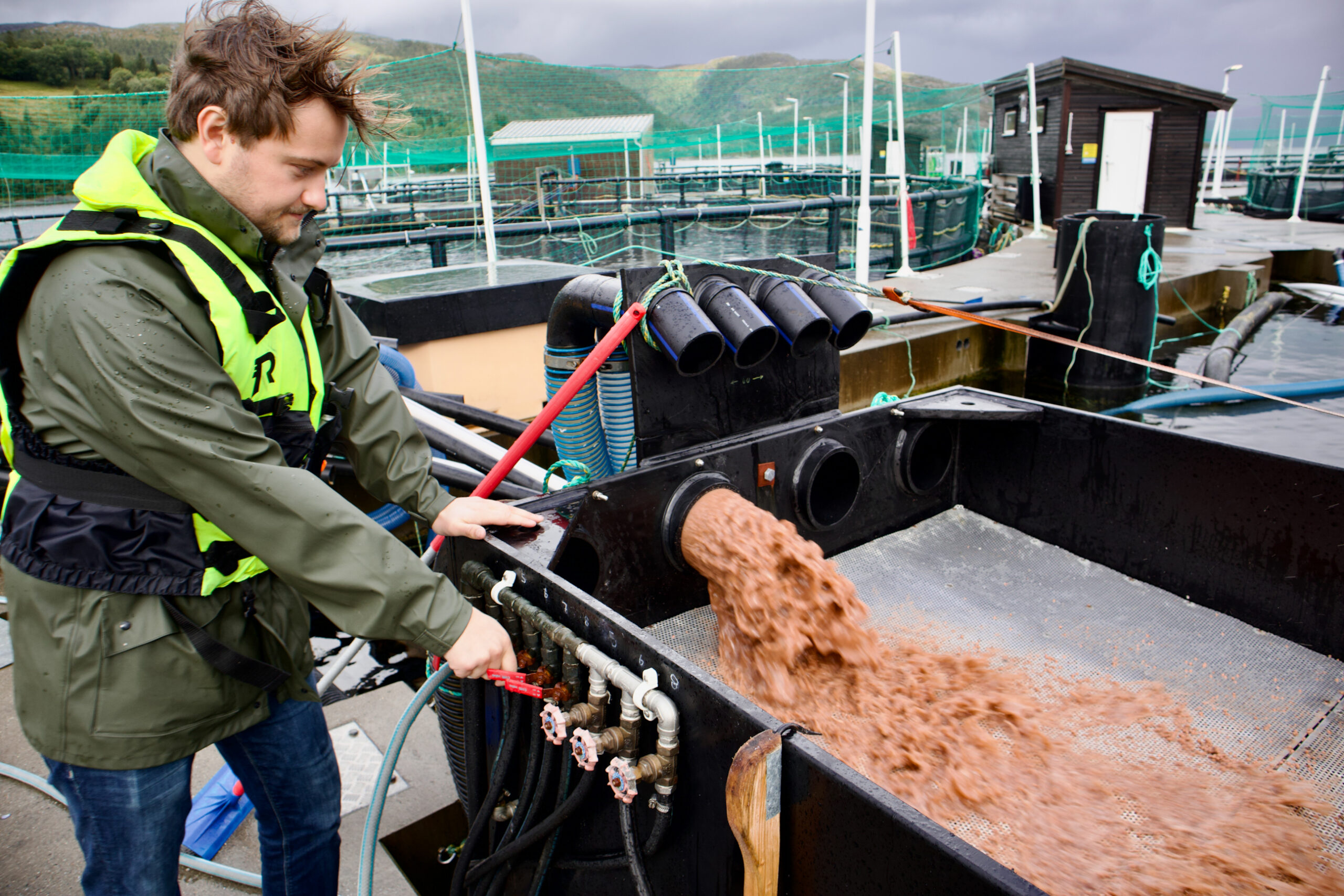
High share of Superior
In the first quarter of this year, Akvafuture harvested well over 2,100 tonnes of eviscerated salmon. It was Mowi who bought and harvested the salmon at the Herøy processing plant. The quality of the fish delivered is superior.
“Our harvest results this year show that 97 per cent of the fish is of superior quality. For the industry otherwise, we hear about figures of around 60 per cent, which are not downclassified. This means that we are able to operate profitably. Good welfare is also good economics. This will only become more and more important, with increased costs for input factors,” he said.
“There are no other places that operate like us. Here we have the world’s largest test facility for closed cages. We expect there is interest in keeping it going. Even if there is talk of technological neutrality, what we have is one way forward that many consider relevant.”
“I expect we will be allowed to continue it, with an extension of the three R&D concessions. An insane competence environment has been built up in closed cages. 30 employees have done this on a commercial scale since 2016 now,” Thomas Myrholt concluded.
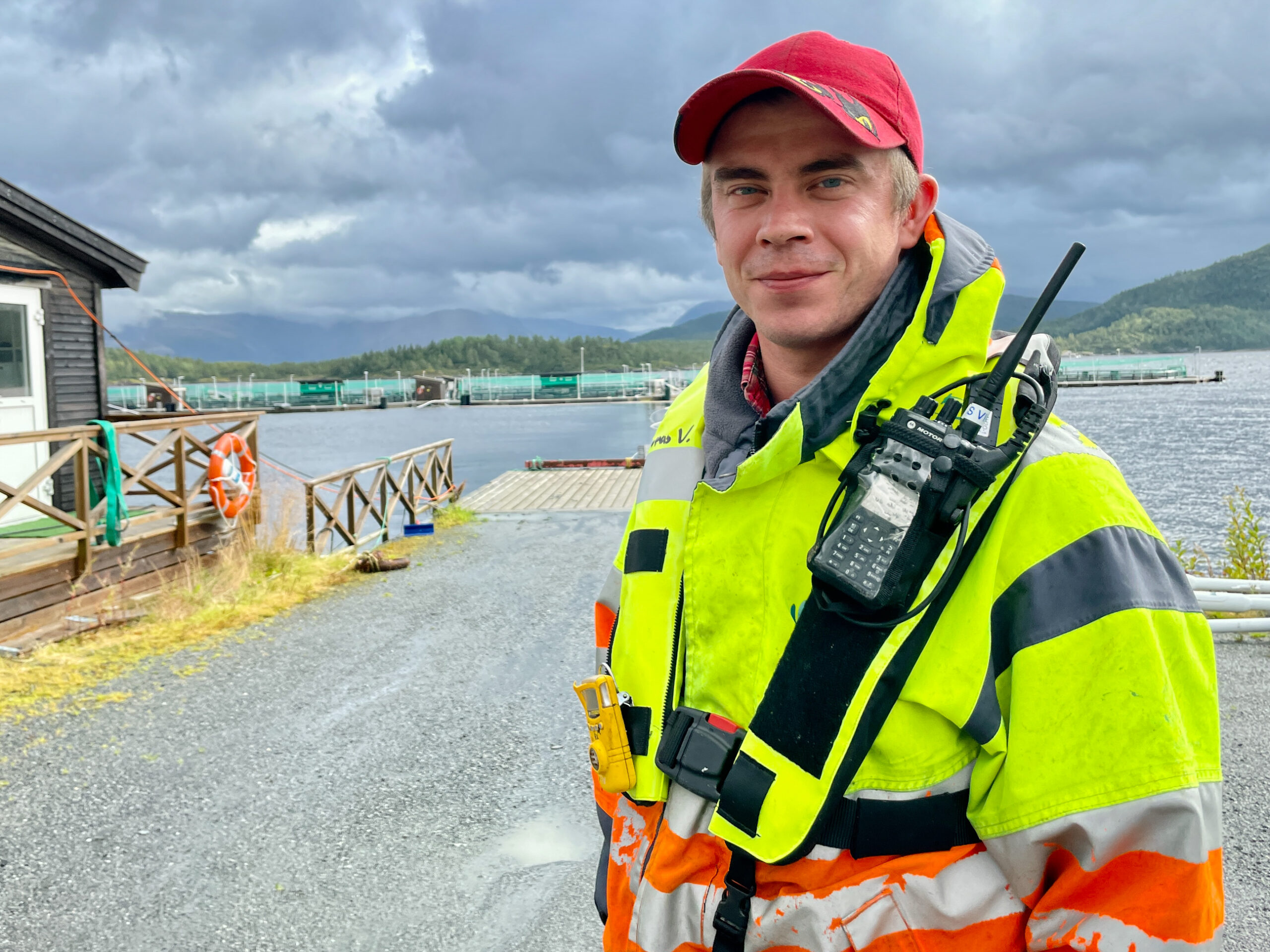